The Benefits of Using Servo Feeders
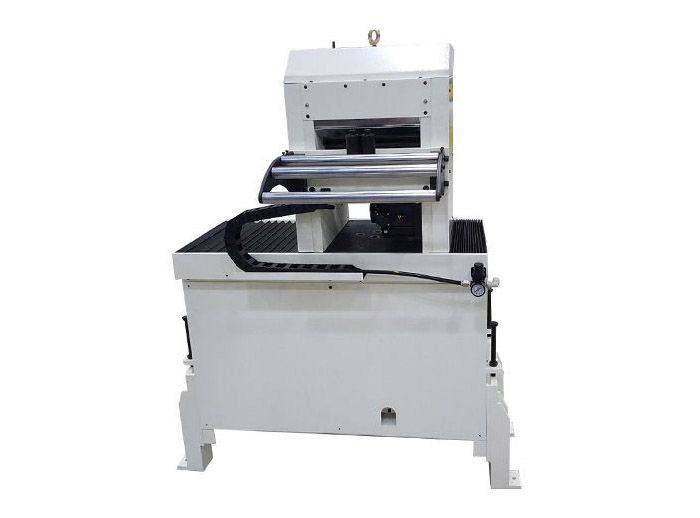
In various industries, such as metalworking, automotive, and electronics, accurate and efficient feeding of materials is essential for achieving high productivity and quality.
In various industries, such as metalworking, automotive, and electronics, accurate and efficient feeding of materials is essential for achieving high productivity and quality. Servo feeders have emerged as advanced automation solutions that provide precise control and reliable material feeding. In this article, we will explore the benefits of using servo feeders and their impact on production processes.
Enhanced Accuracy:
One of the significant advantages of servo feeders is their exceptional accuracy in material feeding. These feeders utilize advanced servo motor technology, which enables precise control over the feeding process. The servo motor ensures consistent and repeatable movement, resulting in accurate placement and positioning of the material. This accuracy is crucial for achieving tight tolerances and reducing material waste in manufacturing operations.
Increased Efficiency:
Servo feeders are designed to optimize productivity and efficiency in material handling. They offer high-speed feeding capabilities, allowing for rapid and continuous feeding of materials. The precise control offered by servo motors enables faster feeding rates while maintaining accuracy. This increased speed and efficiency translate into higher production rates, shorter cycle times, and improved overall operational efficiency.
Versatility and Flexibility:
Servo feeders offer versatility and flexibility in handling various types of materials. They can handle a wide range of materials, including sheets, coils, strips, and more. The feeders can be easily adjusted to accommodate different material widths, lengths, and thicknesses, making them suitable for diverse applications. The flexibility of servo feeders enables manufacturers to adapt to changing production requirements and efficiently handle different material types without the need for extensive retooling.
Seamless Integration with Automation Systems:
Servo feeders are designed to seamlessly integrate with automation systems, allowing for streamlined and synchronized operations. These feeders can be easily connected to other equipment, such as presses, stamping machines, or CNC machines, forming an integrated production line. The integration enables synchronized feeding and processing of materials, eliminating bottlenecks and optimizing overall system performance.
Precise Control and Adjustability:
Servo feeders provide precise control over feeding parameters, allowing for easy adjustments to meet specific production needs. The feeding length, speed, acceleration, and deceleration can be precisely configured using the servo motor control. This level of control ensures consistent and accurate feeding, even when handling delicate or sensitive materials. Operators can fine-tune the feeding parameters based on the material characteristics and production requirements, optimizing the process for optimal results.
Reduction in Material Waste:
The accuracy and precise control of servo feeders contribute to a significant reduction in material waste. The precise feeding eliminates errors and minimizes material scrap, resulting in cost savings and improved material utilization. With servo feeders, manufacturers can achieve tighter nesting of parts, reduce material overrun, and minimize the need for rework or adjustments due to feeding inaccuracies.
Operator Safety and Ease of Use:
Servo feeders prioritize operator safety and ease of use. These feeders are equipped with safety features, such as sensors and guards, to prevent accidents or injuries during operation. Additionally, servo feeders are designed to be user-friendly, with intuitive controls and interfaces that simplify setup, operation, and maintenance. Operators can easily monitor and adjust feeding parameters, ensuring smooth and safe production processes.
Error Detection and Reporting:
Servo feeders often include advanced error detection and reporting features. They are equipped with sensors and monitoring systems that detect abnormalities, such as material jams, misfeeds, or feeding errors. When an error is detected, the feeder can automatically pause or notify the operator, allowing for quick intervention and minimizing production disruptions. The error reporting functionality enables efficient troubleshooting and maintenance, reducing downtime and maximizing productivity.
For more information, please contact us. We will provide professional answers.