Understanding the Coil Blanking Line
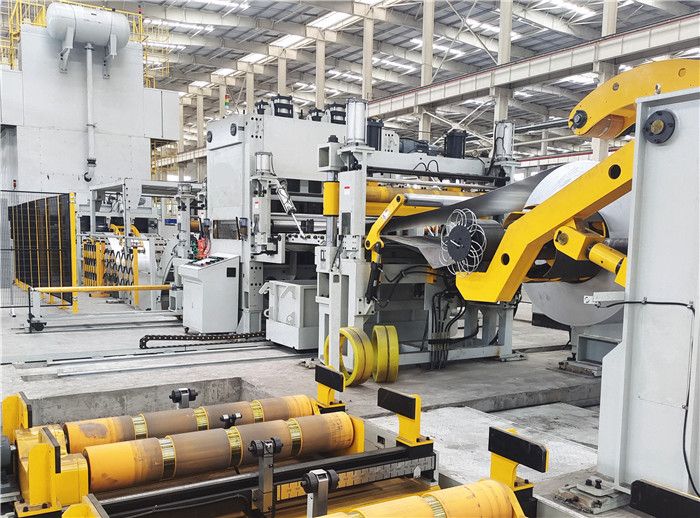
A coil blanking line, also referred to as a blanking line or blanking press line, is an advanced and sophisticated production system widely employed in the metalworking industry. This automated system serves the purpose of cutting flat metal coils into precise shapes and sizes known as blanks.
With the ever-growing demands of the metalworking industry, the need for efficient and accurate cutting processes has become paramount. A coil blanking line seamlessly caters to this requirement by ensuring the production of high-quality blanks, which are integral components in various industries, including automotive, aerospace, and manufacturing.
A coil blanking line, also known as a blanking line or blanking press line, is a highly automated production system used in the metalworking industry for cutting flat metal coils into specific shapes and sizes called blanks. The process of blanking involves shearing or cutting the metal coil to produce individual pieces that will be further processed or used as end products.
The process begins with the unwinding of the metal coil, which is then fed into the line. The coil undergoes a series of precise measurements and adjustments to ensure accuracy and consistency in the resulting blanks.
Once the coil is properly positioned, the cutting process commences. The line employs high-speed mechanical or hydraulic presses to cut the coil into the desired shapes and sizes. The cutting tools used in these presses are meticulously designed and maintained to provide a clean and precise cut without any deformities or irregularities.
In addition to the cutting process, a coil blanking line also incorporates various ancillary operations to enhance the overall efficiency and functionality of the system. These operations may include edge-trimming, hole-punching, notching, or even embossing, depending on the specific requirements of the blanks.Furthermore, the automation aspect of a coil blanking line significantly contributes to its efficiency.
The line is equipped with advanced computer numerical control (CNC) systems, which enable precise control and monitoring of the entire process. This automation eliminates the need for manual intervention, reducing the risk of errors and increasing productivity.Moreover, the utilization of a coil blanking line ensures optimal material utilization.
The line is designed to minimize material waste by strategically positioning the blanks within the coil, maximizing the usage of the available metal. This not only reduces costs but also promotes sustainability by minimizing scrap generation.
Overall, a coil blanking line revolutionizes the metalworking industry by streamlining the production of blanks. Its advanced technology, precision cutting, and automation capabilities contribute to improved productivity, reduced costs, and enhanced quality. As the demands for high-quality blanks continue to rise, the coil blanking line remains an indispensable asset in the metalworking industry, enabling manufacturers to meet the evolving needs of various sectors efficiently and effectively.
The operation of a coil blanking line involves several essential components working in harmony to deliver exceptional results. Let's explore the main components and their functions:
Uncoiler: The uncoiler is the initial component of the coil blanking line. It holds the metal coil and unwinds it in a controlled manner. The uncoiler feeds the coil into the subsequent processing stages.
Straightener: The straightener removes any curvature or bends from the metal coil. It ensures that the coil is flat and properly aligned before it enters the cutting process.
Feeder: The feeder system advances the flat metal coil through the line, positioning it accurately for cutting. The feeder typically utilizes rollers, grippers, or belts to transport the metal coil.
Leveler: The leveler is responsible for flattening and leveling the metal coil, ensuring uniform thickness and flatness across the entire surface. It can have multiple sets of adjustable rollers to remove any residual waviness or imperfections.
Blanking Press: The blanking press is the key component of the line that cuts the metal coil into individual blanks. The press may be hydraulic, mechanical, or servo-driven, depending on the specific requirements and the desired cutting precision. The blanking press operates with a tool and die set, where the die defines the shape of the blank, and the punch cuts through the metal coil to create the blank.
Scrap Removal System: As blanks are cut from the metal coil, scrap or remnants are generated. A scrap removal system, such as a scrap conveyor or scrap chopper, is employed to remove and dispose of the waste material from the line.
Stacker: The stacker collects the cut blanks and stacks them in a neat and organized manner. The stacker can have automated mechanisms or robotic arms to handle and stack the blanks according to specific requirements, such as stack height or orientation.
Control System: A coil blanking line incorporates a sophisticated control system that monitors and coordinates the operation of the various components. The control system ensures precise synchronization of the line's activities, regulates feed rates, monitors safety parameters, and enables operators to make adjustments and optimize production parameters.
Coil blanking lines offer several advantages in the metalworking industry, including high-speed production, consistent accuracy, improved material utilization, and reduced labor requirements. These lines are widely used in various sectors, such as automotive, appliance manufacturing, construction, and metal fabrication, where precise and efficient blanking processes are essential.
In summary, a coil blanking line is a comprehensive production system that transforms flat metal coils into individual blanks through a series of automated processes. It combines components such as uncoilers, straighteners, feeders, levelers, slitters (if applicable), blanking presses, scrap removal systems, stackers, and control systems to achieve high-speed and accurate blanking operations.