High Speed Lamination Stamping Line
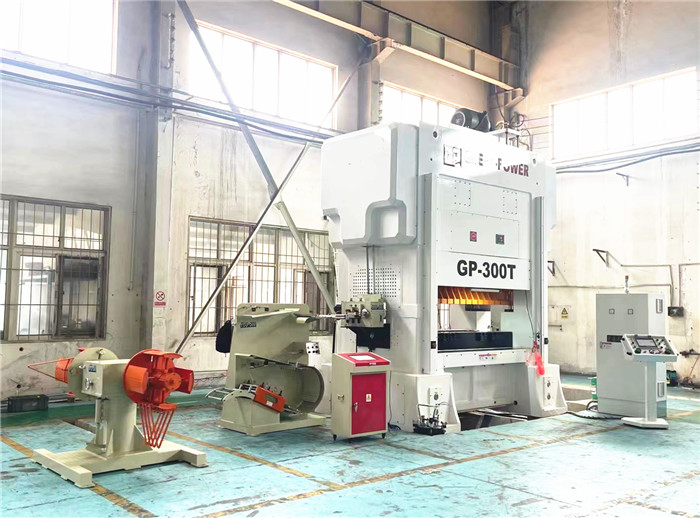
Applicable material
Raw material: silicon steel
Material Thickness: 0.1-2.0m
Coil width: 20-300mm
High Speed Feed Lines configuration
Double Head uncoiler DBMT
S loop Straightener JMS
High Speed Cam feeder GCF
High Speed Press Machine RH
Progressive(For optional)
Stamped Parts Produced By High Speed Lamination Stamping Line
High-Speed Lamination Stamping Line is an advanced forming and processing technology for making the motor stator and rotor laminations, ususlly is equipped with automatic press feeding equipment such as double head decoiler, S loop straightener machine and cam feeder or high speed NC servo feeder.
Main Machines Of High-Speed Lamination Stamping Line
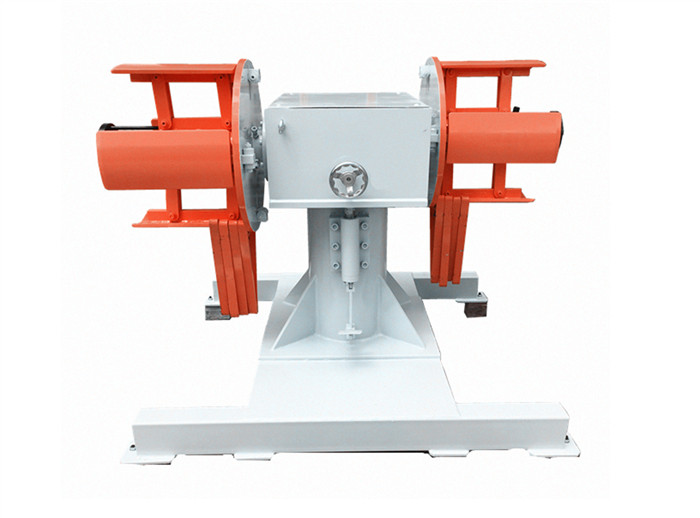
Double Head uncoiler DBMT
Aiming to reduce the time to load a roll to the minimum point, this double head decoiler type drives one of the rolls, as the other one waits as a backup.
When the driven roll is over, the backup roll will be ready to be connected to the driver within a very short period of time. When you connect the new roll to the driver, you will have a long time to load another spare roll. Double head decoiler is an ideal solution for production plants where production speed and continuity are crucial in serial manufacturing. So usually configured with the S loop straightener, high speed gear machine and H frame high speed press machine, it’s usually suitable for motor rotor and stator lamination stamping.

S loop Straightener JMS
S loop High speed straightener is a powerful new equipment for high speed stamping, which can improve the quality and quantity of punch products.It is impossible to produce a good punch by leveling the end of the coil material. Only by leveling the coil material can the stress be eliminated. After leveling by the machine, the material can be corrected to bend downward or flat.The transmission device and frequency converter (cycle control) can synchronize with the punch speed and balance the feeding.
The speed of S loop High speed straightener can reach 60m/min, and usually configured with the double head decoiler machine, high speed gear machine and H frame high speed press machine, it’s usually suitable for EI, motor rotor and stator lamination stamping.
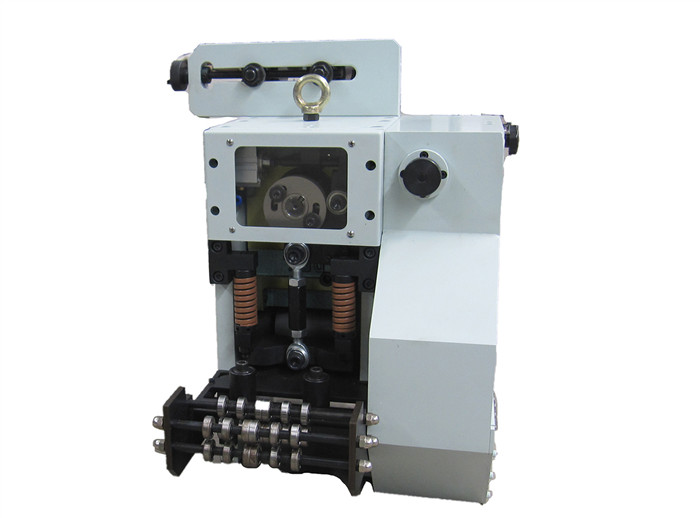
High Speed Cam feeder GCF
High speed Cam Feeder mainly used for motor rotor and stator lamination and EI lamination stamping. Intermittent feeding with rotary cam mechanism. And relay on the stability of the gear transmission mechanism to ensure the feed accuracy.
High speed Gear Feeder is usually working with H frame high speed press machine and double head decoiler machine, the speed can reach 400times/min.
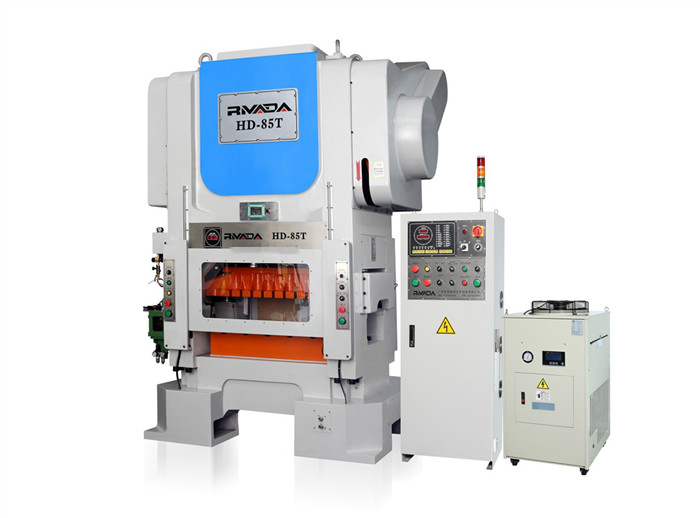
High Speed Press Machine RH
H frame High speed press machine use integrated special cast iron alloys with high rigidity and shock resistance. The slider is designed with a long guide and equipped with a slider balancing device to ensure precise and stable operation. All anti-wear components are electronically timed automatic lubrication systems, such as the lack of lubricant, the punch will be fully automatic stop. Advanced and simple control system ensures the accuracy of the running and stopping of the slider. It can be used with any automated production requirements to increase production efficiency and reduce costs.
High-speed press stroke (speed) per minute is very high, so its higher requirements on the lubrication system, only the use of forced lubrication system, and high-speed presses with abnormal lubrication detection function can effectively reduce the probability of failure of the press due to lubrication.