Types of Coil Feed Line
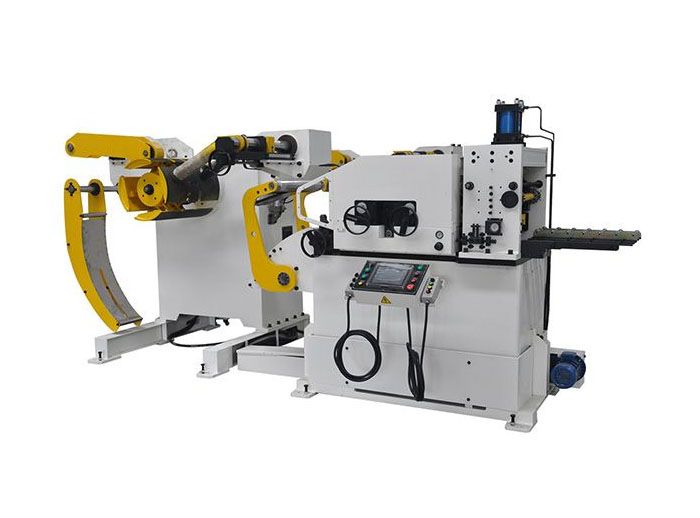
Metal stamping in today's market has never been more challenging. Due to the financial pressure caused by dynamic forces from all sides, metal stamping companies need the most cost-efficient way to produce parts. Of course, economics should also be considered when choosing a coil feed line.
Some space-saving lines may be surprisingly affordable. In terms of capital investment, some are less costly than conventional coilfeed lines with similar specifications. Given the economics inherent in a small footprint - for example, if a larger line requires an extension to the building - a space-saving line may be the most economical option.
The categories of space-saving coil feed lines, from the cheapest to the most expensive, are paddle loop, underslung, and synchronous.
Paddle Loop Line
The paddle loop line include power feeders/straighteners or servo feeders with pull-type straighteners and power reels. The loading carriage is optional. To save space, the loop is developed below the spindle of the reel and is controlled by a laser or loop light system.
If the feeder is equipped with a traction straightener with guided release or a motorised feeder/straightener with guided straightener is used, all upper rolls can be released for guidance, making the line suitable for progressive die applications. The addition of a separate press arm/skimmer/threader/de-bender with exit tilting table provides a hands-free threading process.
Capabilities and limitations are
-The line is compact and varies in length from 16ft to 26ft depending on the pass line.
-It can be sized to fit any coil weight and width.
-Easy to learn operation.
-Optional equipment allows for hands-free threading and pilot release.
-Maximum material thickness is limited to approximately 0.25".
- Material moves on its own at the top of the coil and may cause marks on some highly polished materials.
- The long process must be carefully reviewed to determine if the required speed can be achieved.
Because the process stops and starts, it is not suitable for decorative parts. It is designed for applications where space is limited and where the processes are not too long.
Underslung Compact Line
The system consists of a power feeder/straightener or a servo feeder for a traction straightener with a powered reel and loading carriage (see guide diagram). To save space, the loop is developed below the spindle of the reel and is controlled by a laser or loop light system.
Again, if the system is equipped with a pilot release-capable pull-through straightener or a high-powered feeder/straightener, all upper rolls can release for piloting, thus allowing for proper pilot registration. This feature is particularly useful in progressive die applications. The power rollers included on the loading carriage (or lower coil tongue) and the optional rocker arm assembly with counter bender provide a hands-free method of threading.
System features and limitations include the following.
-It is very compact and typically measures within 15 ft. Range.
-The line length is not dependent on the pass line height as is the case with paddle rings.
- Production line dimensions can be applied to any web weight and width.
-Material can be threaded hands-free.
-Maximum material thickness is limited to approximately 0.156 inches.
-The long process must be carefully reviewed to determine if the required speed can be achieved.
The system is suitable for general progressive die and transfer applications where space is a priority and the number of stages is not too long. The process stops and starts, making it unsuitable for cosmetic applications.
Two-axis synchronous line
The two-axis synchronised line consists of a powered feeder/straightener with powered reel, where the reel and feeder speeds are synchronised. Because the drive of the reel and the feeder straightener are synchronised, this system does not require a loop. Only a small piece of material needs to be wrapped under the spindle to allow a slight slackening to release the pilot.
The web outer diameter (OD) sensor is used to adjust the reel speed according to the web OD, which is necessary when there is no slack loop in the line.
All upper rolls are released for piloting. The pilot release can be pneumatic or hydraulic, depending on the material thickness and yield strength.
The system has several noteworthy features and limitations.
-It is very compact - sometimes less than 20 feet long.
-It can run very thick material - even 1/2 inch thick material and high strength steel (HSS).
- The production line can be sized for any coil weight, width and thickness.
-Can be equipped with auxiliary traction straighteners to accommodate lighter materials.
-The line requires 30% to 60% of the space of a conventional feed line.
- Advanced controls, PLCs and sensors can present potential complications.
- The learning curve for the operator is usually longer than for less complex systems.
-Long processes must be carefully reviewed to determine if the required speed is feasible. Because there are no cycles, long processes must be reviewed on a case-by-case basis to determine if the drive can handle the process, the strokes per minute (SPM) and the available feed window for the application.
The line is suitable for tight space applications running large sizes (0.25" or thicker) of high strength steel and where there is no room for pallets or conventional feed lines. The process stops and starts, so it is not ideal for cosmetic applications.